By Timothy Dale | Published Jul 20, 2023 11:51 AM
We may earn revenue from the products available on this page and participate in affiliate programs. 2 Story Prefab Houses

With soaring real estate prices, it’s no surprise that many people are branching out into new territory when it comes to home construction. Tiny homes enjoyed significant popularity for a period of time, but container homes may become a new trend in residential and business real estate. These homes use new or used shipping containers as the structural basis for the new house.
According to HomeGuide, building and installing a container home costs about $25,000 to $250,000 on average. The wide range is due to the variety of factors involved with planning, building, and finishing a container home, including the size of the home, the number of containers, foundation installation, labor costs, utility installation, flooring, roofing, building materials, permits, and more. Customers can use this guide to find out more about container home cost factors to come up with an accurate budget for the container home construction project.
Building a new home, even if the shell was originally one or more shipping containers, is a complex project that can quickly become costly and overwhelming. Before getting swept away, it’s recommended for homeowners to familiarize themselves with the various factors that can affect the cost of the project, including the size of the home, building materials, and local labor rates.
Shipping containers come in three standard lengths, including 10-foot, 20-foot, and 40-foot. They are typically 8 feet wide and 8.5 feet high, though there are also high-cube containers, which, at a foot taller than standard shipping containers, will offer the homeowner a little extra headroom inside the container home. By cutting and welding the shipping containers, builders can use multiple containers to make larger homes.
However, the larger the home and the more shipping containers required for the construction, the higher the cost of the project. On average, single container models cost about $25,000 to $80,000, while a multi-container home generally costs $80,000 to $250,000. Costs can be lower or higher than these averages.
When installing a new building, adding on to an existing building, or setting up an additional building on the property, the homeowner will need to get a building permit, which can range from $500 to $2,000. Additionally, it’s important for a homeowner to verify that a shipping container home is acceptable for the location according to the local zoning regulations.
While most container home builders will take charge of acquiring the building permits, it’s still important to verify this responsibility before the project starts. Homeowners will also need to budget for the cost of labor, including the best interior designer services, general contractors, architects, draftspersons, plumbers, and electricians. Labor rates vary depending on the local economy and the supply and demand in the area.
In order to prevent the new shipping container home from shifting or being blown over by powerful storm winds, it’s necessary to have a foundation installed to support the container home. Typically, a shipping container home foundation costs between $3,000 to $19,350 on average, though this depends on the size and material used to make the foundation.
The most commonly used material and the most affordable is a concrete slab foundation, which generally costs between $5.75 and $13.50 per square foot. However, homeowners can also opt for pier footings or full crawl space foundations if they are willing to pay a higher price for this part of the project. Pier footing foundations are ideal for homes built on uneven terrain where a basic slab foundation wouldn’t work; the home is built upon a series of vertical piers, which transfers the building load to the soil. A crawl space foundation can be built on sloped terrain and leaves space for storage, wires, or plumbing beneath the home.
The various building materials required to construct a container home can be divided into separate groups for easier selection and budgeting. Doors and windows for container homes are essentially holes cut in the steel exterior, which are then reinforced with additional framing to avoid weakening the walls of the container. Customers can expect to pay about $230 to $820 for each interior door and about $500 to $1,900 for each exterior door. Windows cost a bit less than exterior doors at an average price of $400 to $650 per window.
Homeowners can opt for sloped or flat roofs, depending on personal preference and construction design. The roof of a shipping container is the weakest point of the structure, so it will usually require additional roof structure above the top of the container. Container home roofing typically costs about $3 to $6 per square foot.
A container home without electrical, plumbing, and HVAC is little more than a nicely furnished shipping container. A lot of the electrical, plumbing, and HVAC infrastructure will be installed prior to the delivery of a prefabricated container home, but that won’t be the case for a custom home. Homeowners will want to keep in mind that the installation cost can increase or decrease depending on the electrical, plumbing, and heating and cooling demands of the home.
As mentioned, most of the interior infrastructure will be installed prior to the arrival of a prefabricated container home at the installation site. However, this is not the case for the utilities, which may still need to be extended from the local municipal systems before they can be connected to the new container home. Connecting a container house to local utilities typically involves several additional costs, such as the following.
Given that a shipping container already has a basic structure, the majority of the framing is limited to interior walls, though the doorways, windows, and any other weak points in the structure will require additional reinforcement. Framing the walls of a container home will generally cost about $18 to $24 per linear foot, depending on the height of the ceiling.
Adding insulation to the container home will allow the homeowner and the occupants to enjoy the interior of the home during the freezing cold and the scorching hot months of the year. However, adding many layers of insulation can reduce the size of the living space, so it’s recommended for homeowners to use a spray foam insulation with a high R-value (the measure of how well a building prevents the flow of heat in and out of the home), such as polyurethane spray foam insulation. Homeowners can expect to pay about $0.80 to $4.50 per square foot for container home insulation installation.
After the framework and insulation are in place, the next step is to put in the drywall. Drywall installation for a container home will generally cost about $1.50 to $3.50 per square foot of wall or ceiling. Taping, mudding, and painting the drywall will cost about $1 to $4 per square foot, or about $20 to $50 per hour.
Due to the construction of a prefab container home taking place at a closed facility, the homeowner may not get the chance to work on the drywall or paint the interior of the home. However, if the container home builders allow the homeowner to DIY these finishing touches, it can help to reduce the overall cost of the project.
It isn’t recommended for DIYers to handle the flooring in a container home without prior experience. Homeowners will want to speak to the container home builder to determine if this part of the project will be completed at the factory or on-site after the utilities are connected. Homeowners will need to pay about $6 to $10 per square foot for the material and installation of the container home floor.
The cost of the flooring installation varies depending on the type of material, the size of the floor, the configuration of the home, the number of containers, and the number of stories. Homeowners can check with the container home builder to find out the best type of flooring for container homes and to select a look or design that suits the homeowner’s aesthetic tastes.
The last parts of the home to be installed are usually the lighting fixtures, plumbing fixtures, electrical fixtures, and any appliances that the homeowner has picked out for the house. This is where any slips in the budget can be recovered by selecting inexpensive and affordable fixtures, and appliances to complete the home.
Alternatively, if there is extra room in the budget, homeowners may want to splurge on high-end faucets, lighting fixtures, appliances, and multipurpose furniture that can double as storage space. Adding fold-down tables or a convertible couch that doubles as a bed is a great way to maximize the living space in the container home.
After planning and budgeting for the construction of the container home, there are some additional costs for customers to consider, including the price to purchase land parcels, land clearing costs, grading costs, landscaping services, home insurance fees, and local property taxes.
A shipping container is made for global portability, but when it is reused and converted into a functional living space, it’s necessary to have a place for the shipping container to sit. Usually, this means purchasing a parcel of land (at a cost of about $5,000 to $18,000 per acre) where a permanent foundation can be installed. Ideally, the location will also be close enough to local utilities to make connection quick and more affordable.
Zoning for container homes can vary depending on the location, so it’s important for the homeowner to check the local restrictions and regulations before purchasing land for the container home. Homeowners may also need to have a land survey completed, which costs about $380 to $540 on average. The survey helps to verify that the location is safe for a residential home and identify any site preparations that are required.
After conducting a land survey and purchasing the parcel of land for the container home, the homeowner will need to work with the container home builders to clear, excavate, and level the land. Land clearing costs can range from $1,500 to $6,700 per acre. This service includes removing trees, pulling up stumps, cutting away brush, moving rocks, and hauling the debris to a suitable disposal site.
Before the foundation can be installed, the container home builders will also need to excavate the area to dig a suitable foundation, which costs about $1,000 to $2,500 on average. During excavation, the workers will also grade the land or contour the slope around the proposed site to allow for proper drainage away from the container home. Grading the land costs between $500 and $1,000 to level or contour the area for a container home.
Once the container home is installed, assembled, and connected to the utilities, the land around the home will need to be landscaped to add grass, trees, and other plants to the outdoor space. DIYers with enough time and experience may choose to undertake this project without professional help, allowing them to cut down on the overall cost of the work.
For those who choose to hire professional landscapers, the average cost to install plants and sod around a home is about $4 to $12 per square foot, though this can vary depending on the size of the yard and the type of plants.
Just because the home is made out of new or used shipping containers does not mean that it falls outside of typical home costs. Homeowners will need to get homeowners insurance for the container home, which usually costs from $50 to $150 per month. Some insurance companies may not offer coverage for this type of structure, so homeowners will want to research potential insurance providers before choosing the right company to insure the home.
The homeowner will also need to pay the standard local property taxes to own the land and the container home. Property taxes fluctuate widely between different locations, so before investing in a container home, it’s a good idea for homeowners to check the local property taxes for similar homes or parcels of land to get a better idea of how much they will need to pay in property taxes.
There are two main types of container homes that can be purchased, built, and installed, including prefabricated container homes with relatively fixed sizes, shapes, and construction plans, or custom container homes, which are built according to the homeowner’s personal preference and the input of an architect or design firm.
A prefabricated container home comes with a completely finished interior and exterior. The home also includes all fixtures and appliances, so the homeowner knows exactly what to expect before the container home arrives. Typically, prefabricated container houses cost between $150 and $300 per square foot, though this depends on the size, features, number of shipping containers, number of stories, and any additional costs, such as grading, land clearing, or landscaping.
Homeowners can invest in basic, affordable prefabricated container homes with minimal additions, or they can opt for more high-end prefabricated models that have luxury finishes. However, once a home has been selected, the customization options for a prefabricated container home are minimal.
Custom container homes give the homeowner the ability to select from a range of customization options. Generally, the homeowner will work with the container home builder and an architect or design firm to come up with the final plan for the custom container construction. This type of container home costs a bit more at about $250 to $400 per square foot, but the extra cost may be worth it for flexible size and layout options.
Additionally, custom container homes can be built with two stories, while most prefabricated container homes are single-story. After choosing the exterior, the homeowner can select from a variety of interior finishing options that are only limited by the budget. They may also choose to add container pool costs to their budget for a truly custom home.
There are many reasons to invest in a container home instead of trying to get into the real estate market or spending money on a more traditional home. Container homes are affordable, durable, and offer a level of versatility that is difficult to get with traditional homes. These structures are also environmentally friendly and have a short construction time.
A great reason to invest in a container home is that these structures tend to be more affordable than traditional homes or even some tiny homes. This is because the structure of the home is premade using new or used shipping containers, cutting down on the cost of materials and labor. Additionally, prefab container homes are typically cut, welded, and constructed on a factory floor for an agreed-upon price before the entire home is shipped to the installation site.
Due to this method of construction, there is minimal time for contractors to spend on-site, reducing the labor cost of the project. However, container home builders will still need to prepare the site, install a slab foundation or poured concrete foundation, assemble the container home, and install the utility services.
Another reason to build a container home is the high durability of the structure. Shipping containers are designed for transporting cargo across the world. This means that they are often reinforced to allow multiple shipping containers to be stacked on top of each other without damaging the bottom level or the contents of the containers.
Container homes can be susceptible to high winds, but if the house is secured to a permanent foundation, a well-built container home may even be able to survive close proximity to a hurricane or tornado. Some shipping containers are reinforced with additional steel beams, allowing them to hold up against up to 170 mile-per-hour (mph) winds.
Since shipping containers have been in use around the world for a long period of time, these structures are surprisingly easy to have shipped or delivered to the ideal location. New and used shipping containers can be sent overseas or loaded onto a train or transport truck with minimal issues. Additionally, a homeowner can play around with different shipping container home designs thanks to this versatility.
Beyond the ease of transport and delivery, shipping containers can also be cut and welded to form unique home sizes and shapes that are suited to the homeowner’s tastes. Owners can decorate a single container home as a private guest home or build an expansive container home using four or more shipping containers to ensure there is space for the whole family. In the event they want to hire one of the best home organization services to clear clutter, it will likely cost less than hiring a pro to organize a traditional home.
While a traditional home can take the better part of a year to complete, especially if there are material acquisition issues or weather-related problems that slow the construction process, a container home can be completed in just a few months. Additionally, the majority of prefab container home construction takes place on a factory floor, where upgrades and building code inspections can be completed in a short time frame (if needed—there are some states with no building codes, which may reduce construction time even further).
After the container home is designed, built, and inspected, it is then shipped to the desired location—sometimes in as little as 10 weeks—where a crew prepares the outdoor space, lays the foundation, assembles the container home, and connects the utilities.
Containers homes are typically made with new or used shipping containers. Reusing shipping containers to create homes can reduce the environmental impact of home construction and shipping container waste. Given that there are a large number of old shipping containers that are no longer in regular circulation, repurposing them to make affordable homes reduces the number of unused containers that are simply sitting in storage or collecting rust.
Homeowners can take this a step further by adding energy-efficient features to the container home, including spray foam insulation, green roofing, Energy Star appliances, or even a solar panel system to provide clean energy to the house.
Regardless of shipping container size, the type of foundation, or combined living space complexity, container home construction is not a DIY project. General contractors and other construction professionals with ample experience in the field may be able to build their own container homes, but beyond these knowledgeable professionals, it isn’t recommended for a DIYer to attempt to tackle this project.
The reason DIYers should avoid container home construction projects is due to the wide range of tasks that need to be completed to finish the construction of the home. This includes foundation construction, window and door installation, drywall and insulation installation, plumbing and electrical, connecting the utilities, framing, flooring, landscaping, and painting.
It’s better to leave this work to a team of trained and experienced construction professionals that can help handle zoning issues, get the proper building permit, source materials, draw up a construction plan, lay out a timeline, and complete the container home construction. While the homeowner will need to pay the labor rates for the involved construction professionals, this cost is well worth the high-quality results.
Construction budgets should always have a little extra room in case something goes wrong or an unplanned expense comes up during the project. However, the cost of land and the container home cost can put a heavy strain on the budget for the project, so it’s important for homeowners to think about ways to reduce the overall cost of the container home installation to keep more money in their wallet.
While homeowners don’t need to become experts about every project that takes place around the home, it is recommended to learn more about the actual construction of the container home to ensure that the finished product meets expectations. Customers will want to speak directly to the container home builder in charge of the project, or ask questions to the customer service staff to learn about the construction process, company history, and more. Some of these questions include:
Before investing in a shipping container, it’s a good idea for customers to learn as much as possible about the installation and building process, including insulation, foundation options, building codes, zoning restrictions, building materials, and container home maintenance. Customers can take a look at some of the most frequently asked questions about container home construction and their answers below.
An insulated shipping container can range in cost depending on the type of insulation, the size of the container, and whether it is new or used. On average, an insulated shipping container will cost about $2,200 to $18,000.
There are several types of insulation that can be used to help create a functional living space in a shipping container, including fiberglass cellulose, Rockwool, polystyrene, wood fiber, and polyurethane spray foam insulation. To conserve interior space and reduce heat transfer through the walls of the container, polyurethane spray foam insulation is a good choice.
The cost of shipping container insulation, especially for larger containers, can get expensive, depending on the type of insulation. The cheapest option is polystyrene boards, which cost about $0.25 to $0.50 per board foot, though this insulation doesn’t have a high R-value. Alternatively, spray foam insulation costs $1 to $2 per square foot, but tends to function better as an insulator in container homes.
In order to properly insulate the shipping container without taking up a lot of interior space, homeowners will want to invest in a type of insulation that can be applied in a thin layer but still perform adequately due to the high R-value, such as polyurethane spray foam.
Shipping container houses typically have 14-gauge corrugated steel walls that are 0.075 inches thick, with frames, pillars, and rails made of 7-gauge tubular steel at a thickness of 0.187 inches.
Alternative living spaces such as shipping container homes can be kept cool by installing container vents, investing in a heatproof roof installation, adding extra insulation, installing an air conditioner or dehumidifier, sealing the windows and doors, or setting up the shipping container on a plot of land in a shady location.
Sources: HomeGuide, Angi, Mobile Modular Portable Storage
Articles may contain affiliate links which enable us to share in the revenue of any purchases made.
Registration on or use of this site constitutes acceptance of our Terms of Service.
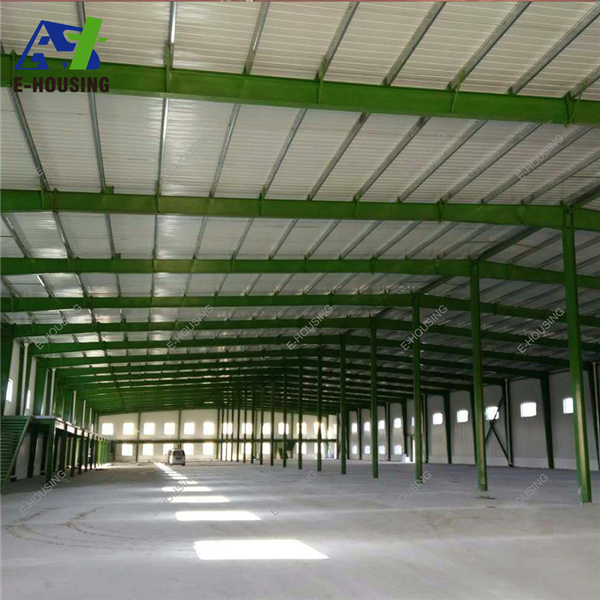
3 Bed Prefab House Prefabricated © 2024 Recurrent. All rights reserved.