José Garcia, plant manager, welcomed Steinert to talk about the company’s development. He emphasized their investment in state-of-the-art technologies and infrastructure, and their status as a pioneer, having implemented an integrated system of collection and smelting of scrap aluminium cans since 1991.
With 4 smelting plants and a processing capacity of more than 300 thousand tons of aluminium per year, Latasa Reciclagem stands out as the largest aluminium recycling company in the country. In addition, its diversified product portfolio serves various industries, such as automotive, steel, metallurgy, packaging, and consumer goods. Steinert visited the site in Pindamonhangaba, São Paulo, to learn more about Latasa’s journey of innovation and technology, which has been undertaken with the aim of recycling 100% of the aluminium processed. Aluminium Melting Rotary Furnace Manufacturer
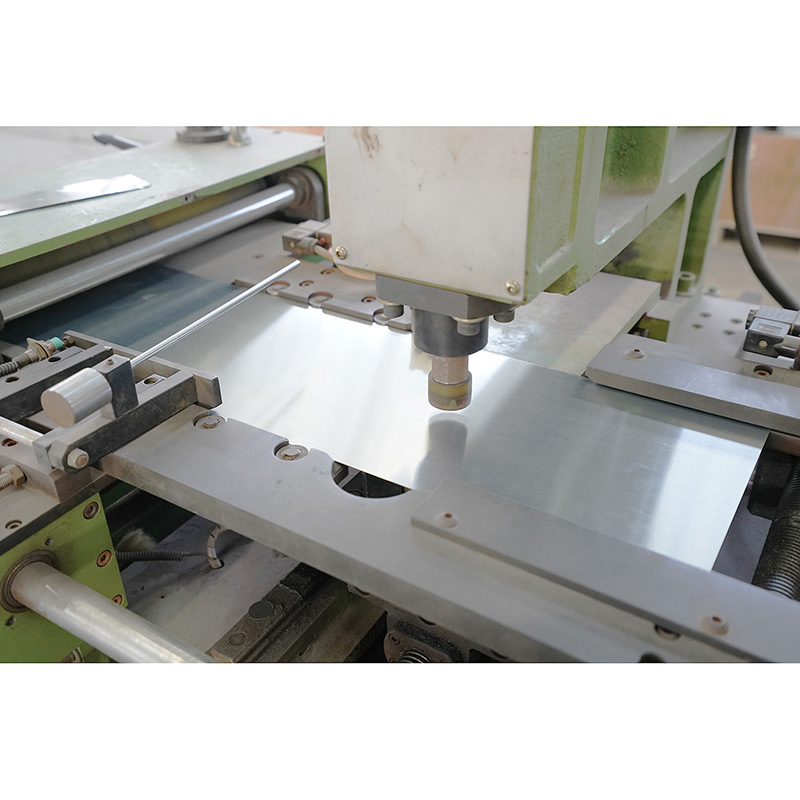
Latasa uses a process known as “Garimpeiro Urbano” (Urban Mining), present in 15 Brazilian states, which represent 96.07% of the country’s aluminium can generation. This initiative involves 22 non-ferrous metal collection centres, working together with local suppliers of recyclable material, including cooperatives, municipalities, and small suppliers.
Latasa’s final production follows the current Aluminium Scrap Classification Table, which lists the names and characteristics of 20 types of scrap material identified in the domestic market. The Aluminium Scrap Classification Table was prepared by ABAL (Brazilian Aluminium Association) and follows recommendations from the Institute of Scrap Recycling (ISRI).
In mid-2019, multinational aluminium manufacturing company, Novelis, approached Latasa looking for a new type of scrap material to work with, Taint/Tabor. According to ISRI specifications, Taint/Tabor is described as clean mixed old alloy sheet aluminium. To generate the required high purities of the desired products, a recycling process is needed, that can separate different aluminium qualities.
“When we got to the stage that involves cleaning the scrap, we already knew about magnetic separators (of various types), screens, Eddy Currents and other methods. However, it was not just cleaning that was required, but separating the scrap by different densities or by type of chemical composition. That’s when we turned to Google and found Steinert, where we discovered several types of equipment, and the one that interested us the most was the X-ray”, explains Latasa’s plant manager José Garcia.
In August 2021, the first tests were carried out with Taint/Tabor scrap. The results met the expectations of the equipment that Latasa and Novelis needed. The partnership with Steinert was consolidated and, in March 2022, the Taint/Tabor Processing Line was inaugurated at Latasa Recycling Plant 1 with the implementation of Steinert KSS | XT LI.
For the processing of all types of collected materials, and with the aim of achieving pure and furnace-ready aluminium, Latasa makes use of an automated plant with Steinert separation technologies in operation.
The Latasa plant in Pindamonhangaba operates:
§ Steinert UME – Overbelt magnet for the separation of ferrous metals from aluminium scrap.
§ Steinert EddyC – Eddy current separator to clean the non-ferrous metals from non-metallic residues.
§ Steinert KSS | XT LI (X-ray transmission + 3D laser + inductive sensors) – Sorting System with a combination of sensors that separates impurities from aluminium and produces furnace-ready aluminium.
With input material received from different collection sources, the mechanical processing begins with two stages of shredding. Subsequently, the material fractions are screened into different particle sizes, namely: 5 mm to 15 mm and 15 mm to 80 mm.
After this step, the material undergoes the separation processes, passing first the Steinert UME for the separation of ferrous materials, and then onto the separation of non-ferrous metals from non-metallic residues with the Steinert EddyC eddy current separator.
The material produced by the eddy current separator is forwarded for selection and separation with the Steinert KSS, of clean aluminium from other materials (remaining heavy metals), using the Steinert KSS sensor combination technology (X-ray transmission + 3D laser + induction). At this stage, the aluminium is already extremely pure. Material that has paint is subjected to a process called decoating. Following this, it goes to the oven, and the paint-free material is ready to be melted.
The use of an automated plant and advanced technologies demonstrates Latasa’s commitment to adopting sustainable practices and maximizing the recovery of valuable materials during the aluminium recycling process.
A study of the company’s process and tests were carried out at the Steinert Latinoamericana Test Center in the metropolitan region of Belo Horizonte. As well as analysing the material samples, the dimensions, feasibility of application, and the choice of the most suitable technology were also analysed. The result was that Steinert’s Combined Sensor Sorting was found to be the best solution. With the implementation of Steinert KSS | XT LI technology, Latasa has made a leap forward in innovation and efficiency in its process of separating and recovering aluminium and valuable materials.
This technology is applied to maximize the recovery of earnings, giving maximum value to each product and reducing the amount of waste material. “The big difference is the ability to perform unique separation for each material to meet the needs of each customer. We have great flexibility in creating a product according to the application that the customer is seeking. We depend on a few external processes, which would only be the physical preparation of the material with the corresponding granulometry for use in the equipment. This is the key differentiator: having low operating costs and delivering such high flexibility to the customer, allowing them to choose several applications”, guarantees Vinícius Souto – Managing Director of STEINERT Latinoamericana.
Making operational costs feasible and facilitating the sorting of different materials under different criteria in a single piece of equipment, the use of STEINERT KSS was the step Latasa was looking for to innovate in the sector and further improve its processes.
Steinert has enjoyed a consolidated partnership with Latasa since 2019. We believe in the potential of applying separation technology to improve aluminium recycling, and we walk side by side, consolidating significant gains in the sector and outlining plans for the future.
With a team of specialists in São Paulo, Steinert Latinoamericana maintains close contact and reliable face-to-face and/or remote support for customer needs. This proximity and commitment ensure assertiveness in planning and the results achieved.
Thinking about the future and further improving its results, Latasa aims to invest in the innovation and automation of other plants.
Latasa demonstrates a solid commitment to sustainability and plays an important role in the production chain in the aluminium recycling sector. We are proud of this partnership and proud to work together promoting the circular economy and the reduction of environmental impacts caused by primary aluminium production.
Save my name, email, and website in this browser for the next time I comment.
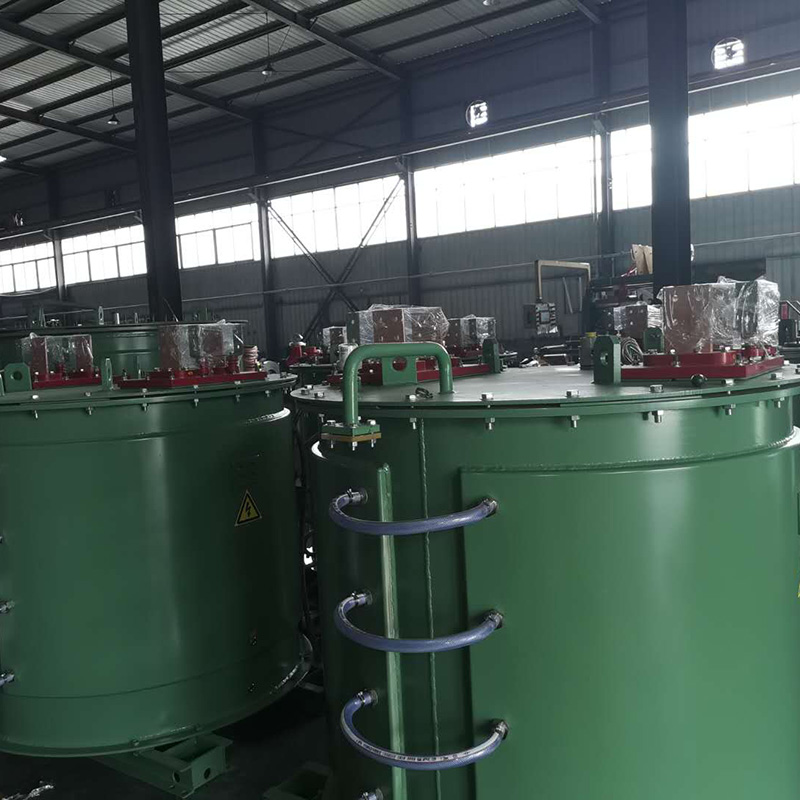
China Brass Furnace Factory This site uses Akismet to reduce spam. Learn how your comment data is processed.