It’s no secret that fiber optic cabling has become a major product category for the AV installation industry, but oftentimes proper training and education are not readily available. To make things easier on small businesses and installers, CE Pro has teamed up with VChung to deliver a thorough guide to fiber optic cable splicing that covers both Mechanical Splicing and Fusion Splicing in the field.
First, let us understand the meaning of the term “splice.” According to Cambridge Dictionary, to splice means to “join the ends of something so that they become one piece.” So in essence, fiber optic splicing is a process used to join two separate fiber optic cables together. 15u Data Cabinet

There are numerous use cases for fiber optic splicing. Through splicing, fiber optic technicians can extend the length of the fiber to make it long enough for use in a required cable run. As fiber optic cables are generally only produced in lengths up to around 5km, so when lengthier connections are needed, splicing two cables together becomes necessary.
Related: 13 'Horrorific' Wiring Jobs That Will Haunt Integrators' Dreams
So when the cable runs are too long for a single length of the fiber, or if there’s a need to join two different types of fibers, such as a 48-fiber cable to four 12-fiber cables, splicing is the answer. Splicing is also used to repair severed fiber optic cables that are buried underground or to rejoin fiber optic cables when inadvertently broken.
While there’s another method of joining fibers known as termination or connectorization, splicing is usually the preferred way to join two fiber optic cables as it results in a lower light loss (attenuation) and back reflection than connectorization.
Moreover, splicing renders a permanent or relatively permanent connection between two fiber optic cables. Some companies do offer fiber optic splices that can be disconnected at will, however, they are typically not meant for frequent connection and disconnection.
In an ideal world, a fiber optic installation would consist of long, continuous cable runs from one place to another. However, in reality, fiber optic cable splicing is inherently necessary and always used when designing, installing, and maintaining a reliable communications network.
With fiber-optic connections becoming increasingly mainstream, the ability to accurately perform fiber optic splicing is becoming more and more important. As of now, fiber optic splicing can be carried out using one of two methods: fusion splicing and mechanical splicing.
Before moving forward with a fiber optic installation, it is vital for integrators to have a fairly good understanding of both methods. This would help determine which technique will work best for your company’s long-term goals and fit your performance and budget requirements.
This fiber optic splicing technique involves the precise alignment of two fiber optic cables, held in place by a self-contained assembly rather than a permanent bond. A mechanical splice is designed to hold two fiber cables in a way that allows light to pass through seamlessly, with a typical loss of around 0.3 dB or 10%.
In this process, the technician must use an alignment device along with an index matching gel. The gel must have a similar refractive index to enhance the light transmission across the joint, with minimal back reflection.
Mechanical splicing is usually used when splices need to be made quickly and easily, for instance, to temporarily connect cables during installation. That’s because mechanical splicing can be easily disconnected if the need arises and you don’t require costly apparatus to perform the splice.
The other method to join two fiber optic cables together — and this time we’re talking a permanent connection — is fusion splicing.
In this technique, a machine or an electric arc is used to produce heat and fuse/weld glass ends that are precisely aligned together for continuous transmission of light. This translates to a much lower attenuation of around 0.1 dB.
Fusion splicing produces a reliable joint with low insertion loss and nearly zero back reflection when done correctly, and thus, is more widely used than mechanical splicing. For example, it’s used in long high data rate connection lines that, once installed, are unlikely to be modified.
One major reason for choosing a particular method over the other is budget.
Mechanical splicing has a low initial investment but costs more per splice. Whereas the cost per splice for fusion splicing is lower but the initial investment is much higher, starting at ten times higher than mechanical splicing, based on performance requirements and features of the fusion splicing machine used.
Talking about performance, the decision comes down to the project you are working on. As outlined earlier, fusion splicing produces much lower loss and back reflection than mechanical splicing, so if you need a permanent joint with minimal attenuation, fusion splicing is the heftier investment you’re looking at.
Also, fusion splices are generally used with single-mode fiber while mechanical splices work with both single and multi-mode fiber. (Learn more about types of fiber optic cables and other fiber optic essentials here.)
All things considered, mechanical splicing works well only for quick restoration and temporary connections where a somewhat notable loss is acceptable. Fusion splicing, though costlier, is far more popular as it provides the lowest insertion loss, back reflection, and the strongest joint between the fibers.
Now that you’re aware of what mechanical splicing is, let’s take a look at the basic steps involved in mechanical splicing.
The first step is to neatly strip the fibers of its protective coatings, jackets, tubes, strength members, etc, leaving nothing but the bare fiber cores.
You’ll know if it’s done right when you see the bare fiber in the section where the cable was stripped. Also, make sure the cables are clean.
After stripping your fiber optic cables, the next step is to break your cables using a fiber cleaver. Use the cleaver carefully to create a small, clean cut on the cables with ends perpendicular to the fiber axis.
Unlike fusion splicing, you don’t need to use heat to join the fibers.
In essence, you just have to precisely position the fiber ends together in the mechanical splice unit. The index matching gel inside the equipment will do the heavy lifting for you, linking the light in the ends of your cables. If you’re using an older unit, you may have to use epoxy instead of an index matching gel to align the fibers properly.
Once you’re done with these three steps, place the fibers in a splice tray and then inside a splice closure.
As such, the completed mechanical splice renders its own protection for the splice. But make sure to seal the cables carefully, as this will prevent your cables from experiencing moisture damage.
Fusion splicing is similar to mechanical splicing in some regards, but with one major difference — you need to use a high-tech tool known as fusion splicer. This tool is responsible for perfectly matching the fiber ends by melting and fusing them together.
Here are the steps involved in fusion splicing.
Before you strip fibers, add a protective sleeve to the fiber.
Then, as with mechanical splicing, strip the protective polymer coating around the optical fiber using a mechanical fiber stripper, until you reach the bare fiber cores. Don’t forget to clean your stripping tools before you start the process.
Using 99.9% isopropyl alcohol (IPA) wipe, clean the bare fiber. Do it twice, using a different part of the wipe for the second round of cleaning.
Once cleaned, avoid touching or putting the fiber into contact with any potentially contaminated surfaces or materials.
Next, use a fiber cleaver to render a clean, mirror-smooth break on the cables with ends perpendicular to the fiber axis. Using a good fiber cleaver is vital to an effective fusion splice.
You are now ready to fuse the fibers together using the fusion splicer. This step involves the alignment of the fibers followed by heating to melt the fiber ends and fuse them.
Alignment can be manual or automatic depending on the type of fusion splicer you use. Once the end faces of the fiber are perfectly aligned and centered on the electrodes, the splicer unit uses an electric arc to melt the two fiber ends and permanently fuse them together.
If the fusion splicer stops the process, it may be because of any of the following issues:
If the fusion is successful, the splicer will estimate and report the attenuation in dB.
A typical fusion splice has a tensile strength between 0.5 and 1.5 lbs and will not break during normal handling. Even so, it’s a good idea to provide protection from bending and pulling forces and ensure the fiber doesn’t break during routine use.
So, after the fibers have been successfully fused together, it’s time to protect the fused fiber by either re-applying a coating or by using a splice protector.
You can use heat shrink plastic, silicone gel, or mechanical crimp protectors to secure the splice from external damage and breakage.
To ensure quality splicing, you must visually inspect the splices you made. You’ll likely find some flaws in the splices but as long as it does not affect the optical transmission of your cables, it’s all good.
Here’s how good splices look like:
That being said, not all splicing flaws are acceptable. If there are black spots, lines, bubbles, bulges, or shadows, rework may be required. To ensure optimal quality of transmission, never rework the splice more than twice.
Here’s how bad splices look like:
As with anything, practice makes perfect. And knowing some fiber optic splicing best practices can go a long way in completing better splices with minimum back reflection and maximum transmission efficiency.
Here are three easy yet effective ways to perform better splicing:
Considering the microscopic nature of fiber optics, know that particles not visible to the naked eye could cause huge problems in terms of cable performance.
There’s no such thing as “excessive cleaning” of your fiber optic tools, and investing some effort in keeping your splicing tools immaculate will save you a lot of time and money in the long run.
The cleaver is the most valuable tool you need to complete effective fiber optic splicing.
For mechanical splicing, you must ensure the proper angle of end faces, otherwise, there’ll be excessive light escaping into the air gaps between the two fibers. Sure, an index matching gel will help minimize light escape, but the importance of a high-quality cleaver cannot be overlooked.
For fusion splicing, your cleaver plays an even more important role to achieve the incredible low attenuation of less than 0.1 dB.
Simply put, if you don’t maintain your cleaver, the fiber ends may not fuse together properly, resulting in high attenuation and back reflection.
The best way to clean and maintain your cleaver’s quality is to simply follow the manufacturer’s instructions.
Don’t start altering the fusion parameters on the splicer whenever there is a hint of a problem, as you might lose your desired setting.
Broadly speaking, fusion time and fusion current are the two main parameters whose variables can be varied to produce strong splice results. Change only one variable at a time in a methodical way until you find the right fusion parameters for your fiber type.
This story is a contribution courtesy of those at the VChung fiber optic cable company.
If you enjoyed this article and want to receive more valuable industry content like this, click here to sign up for our digital newsletters!
News Products Projects Companies Downloads Webcasts Podcasts Events
About Contact Us Customer Service Advertise with Us
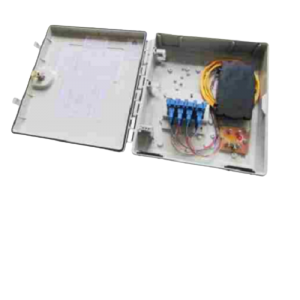
12 Port Sc Fiber Patch Panel Twitter Facebook LinkedIn YouTube RSS Feed