Space exploration requires robust, reliable, and long-lasting technologies, especially for human-safety-critical systems utilized on extended missions. While the safety-critical systems have traditionally leveraged simple-and-dependable, tried-and-true solutions, significant performance and SWaP (size, weight, and power) gains can be realized by leveraging the vast improvements in computing power and electronics’ reliability in the past few decades.
These advances have shifted the focus toward digital and software controls, enabling step changes in performance. Hydraulic or pneumatic legacy systems are replaced with electrical systems and mechanical means of flow control, such as valves are replaced with variable speed motors. Angular Contact Bearing
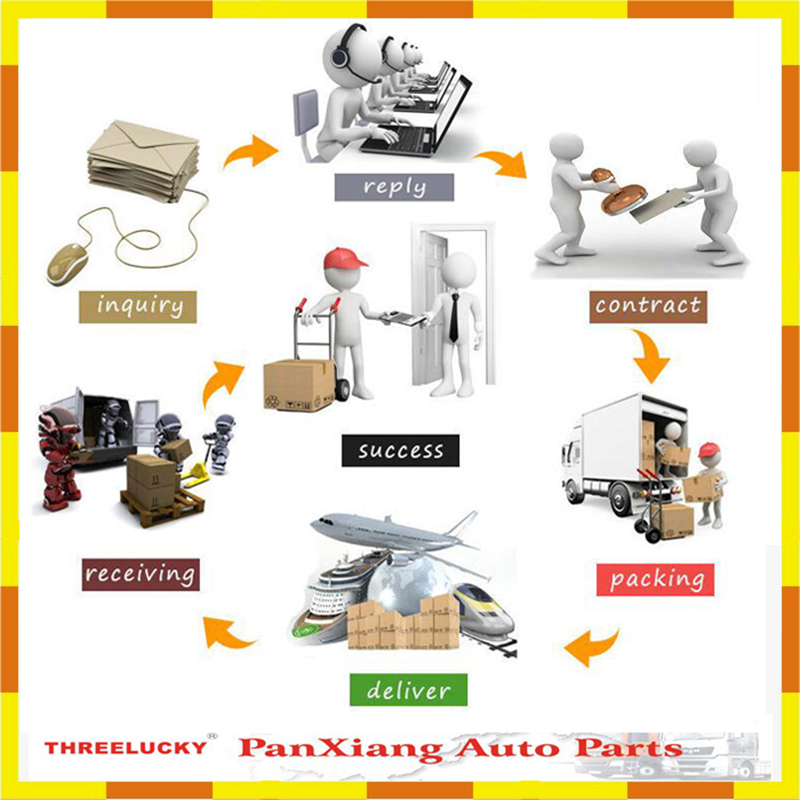
This shift of electrification and optimization is highlighted by some of the recent improvements in the environmental controls on the International Space Station (ISS). The makeup of the breathable atmosphere must be managed, and trace contamination must be reduced to acceptable levels.
The Four Bed Carbon Dioxide Scrubber (FBCO2) system currently in advanced development and testing on the ISS is the latest iteration of the CO2 removal system. The FBCO2 system draws air from the cabin and separates water and CO2, which can then be reused for other purposes or vented as waste. Within the FBCO2 system, the Calnetix In-line blower/circulator is the mechanism which drives air flow through the system.
The In-Line blower system, which includes a compact blower on magnetic bearings and an integrated dual controller, leverages a variable high-speed permanent magnet (PM) motor and active five-axis active magnetic bearing (AMB) system. This system represents a step change toward electrification and optimization. Previous CO2 removal solutions utilized passive gas foil bearings that float the rotor on a layer of gas once the rotor is spinning.
While this was a simple solution from a controls perspective and requires no electronics to manage the bearing system, gas bearings can be susceptible to contaminants in the process airstream, are prone to wear with many start/stop cycles, and require a minimum process gas pressure and rotor speed to operate. Conversely, AMBs require relatively complex electronic and software controls, but can function at very high speeds, provide significantly improved life with no mechanical limits on cycles, are tolerant to particle contaminants in the process airstream, and can operate when exposed to vacuum.
The main design challenge was to fit the new magnetic bearing blower into the same space as the gas-bearing-supported heritage blower. The AMB system with position sensors and backup bearings had to be miniaturized to fit into a highly constrained space.
To circulate environmental air through the FBCO2 system, the blower leverages an overhung radial impeller spinning at up to 60,000 rpm. From the impeller, flow is directed through the housing and around the centrally located motor section. Keeping the motor effectively sealed from the process flow keeps the motor and bearing components free from erosion or accumulation of contaminants.
Process flow around the motor and magnetic bearings cavity also provides heat rejection for thermal management of the stator. Backup bearings provide a mechanical backup function in the case of shock loads exceeding the load capacity of the magnetic bearings, or any time the active magnetic bearing system experiences a fault or loss of power.
To take advantage of the frictionless magnetic bearings system, the PM motor can operate at very high speeds, providing improved volumetric and gravimetric power density. The radial flux surface-mount PM rotor utilizes a carbon fiber sleeve to provide rotor-dynamic stiffness and magnet retention while providing improved permeability. With windage as the only major mechanism for loss, a motor such as this can exceed 98 percent efficiency.
From a controls perspective, the AMB is significantly more complex than legacy mechanical bearings or air bearings. Speed and position sensors in the stator are utilized to determine velocity and orientation of the rotor. Electromagnetic actuators provide the force to center the rotor, counteract dynamic loads, and safely maintain rotor position with five axes of control. Permanent magnets can be used to bias the AMB system to offset static loads and reduce control current.
The Calnetix dual electronic controller ties all of this together, taking inputs from the sensors, driving the speed of the motor, and controlling the relative position of the rotor. The added complexity comes with the advantages of the ability to actively tune the performance of the motor, real-time motor status monitoring, and prognostic health monitoring of the blower as well as the connected system.
Sensors in Inflatable Space Habitats
Wireless Sensor System to Detect Leaks on the International Space Station
Long-duration human habitation in space or on other planets will require efficient, robust, and highly reliable solutions for the processing of breathable atmosphere and other health-critical systems. “The unique blower system was successfully installed by NASA on ISS and has been operating continuously since February 2023,” said Vatche Artinian, CEO, Calnetix Technologies.
“This is the first time a five-axis, magnetically levitated system has been commissioned for use in an orbital application and shows promise as a technology, which can be used across many other applications, such as fluid pumps, reaction wheels, and gyroscopes that challenge conventional bearing technologies,” Artinian added.
Following the validation phase in the current ISS system, AMB and related high-speed PM motor technologies could further be utilized in future space missions, such as Artemis, Orbital Reef, and Mars missions.
This article was written by Matthew Farides, Director of Business Development, Calnetix Technologies (Cerritos, CA). For more information, visit here .
This article first appeared in the August, 2023 issue of Tech Briefs Magazine.
Read more articles from this issue here.
Read more articles from the archives here.
Reaching for the Moon: Astrobotic Peregrine Mission One
4 Predictions for 2024: AI Set to Supercharge Robotic Automation
How Corning’s Hyperspectral Imaging in the Sky Sees the Unseen
How Much Do You Know About EMC/EMI?
Will It Trigger a Manufacturing Revolution?
How Cloud Technology and AI Drive a More Productive Future
Additive Manufacturing for Aerospace: Taking Your Production to New Heights
Leveraging Today’s Extrusion Technology: Hollows and More!
Hydrogen’s Promising Role in Heavy-Duty Vehicles
Here's an Idea: A New Minimally Invasive Approach to Spinal Cord Injury
NVH Prediction in Electric Powertrains: Considering Inverter and Motor Spatial Harmonics
Understanding Technological Advancements in IR Detection Modules
A Green Li-ion Battery-Recycling Method
Reaching for the Moon: Astrobotic Peregrine Mission One
Answering Your Questions: Lithium-Air Battery vs. Lithium-Ion
Commercial Lunar Landers Ready for the Moon
Comparison Between Wave Soldering and Reflow Soldering
Printed Electronics: The Future Is Flexible
5Ws of the Eye-Safe Laser
Polycarbonate Seen As Top Choice for LED Lighting
The Modern Industrial Workhorse: PID Controllers
The Basics of Encoder Selection
How Much Do You Know About Predictive Maintenance?
Smart Sensor Technology for the IoT
Networking the IoT with IEEE 802.15.4/6LoWPAN
Robotic Additive Manufacturing of Large Steam Turbine Blades
Laser Beam vs. Electron Beam Welding Which process works best for what?
A Precision Arm for Mini Robots
Mechanical Carbon Materials for Aircraft Seal Applications
Brushless Motors for In-Tank Fuel Pumps
Here's an Idea: A New Minimally Invasive Approach to Spinal Cord Injury
Here's an Idea: Human Factors in Drug Delivery
Here's an Idea: Powerful Sensors for the Eye
By submitting your personal information, you agree that SAE Media Group and carefully selected industry sponsors of this content may contact you and that you have read and agree to the Privacy Policy.
You may reach us at privacy@saemediagroup.com.
You may unsubscribe at any time.
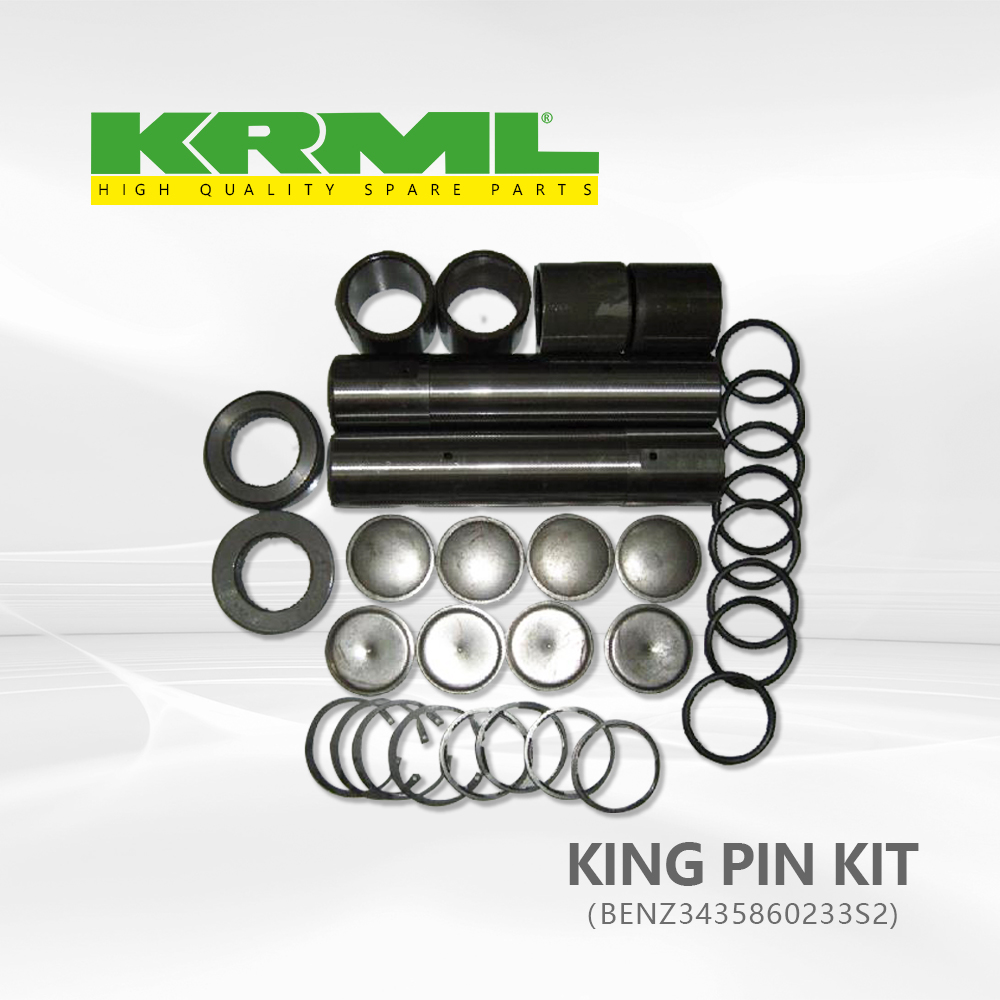
Hanger Bearing © 2009-2024 SAE Media Group